|
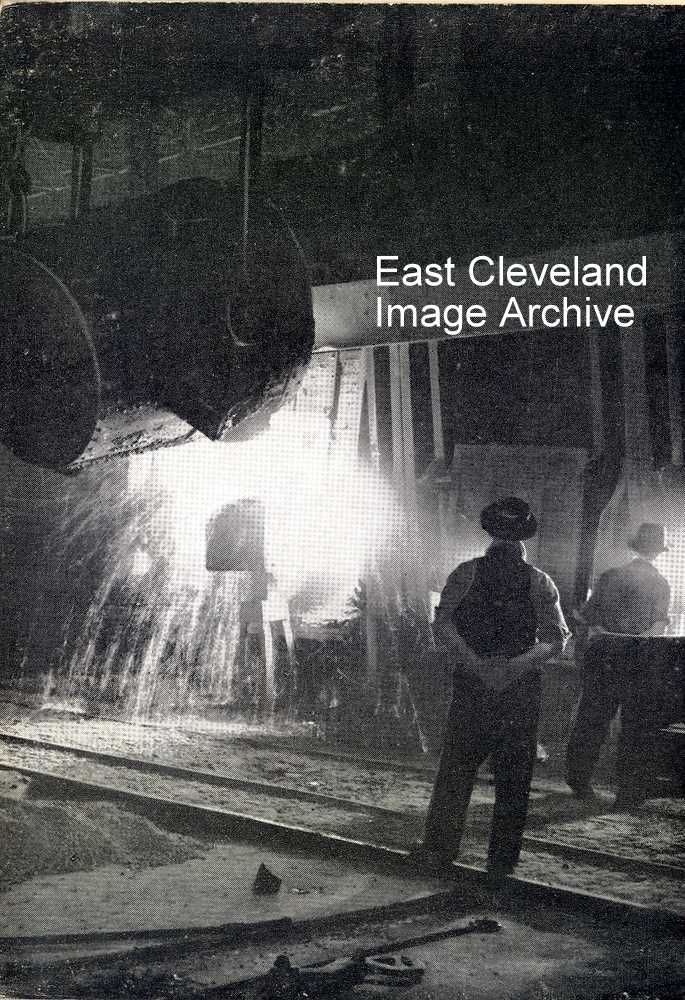
This was always a beautiful sight to behold – a portable spout was placed into the gaping door (usually an end one) of the furnace and with its siren whooping the crane would manouevre the sizzling pot of iron over it, then delicately empty the pot into the furnace – bringing memories of bonfire night! Eric Johnson told us: “The chap in the foreground with his back towards the camera is Sid Carter, also note the sample pot”. Rodney Begg has advised: “I think this must have been taken on my shift (’C’ shift I think it was ), because I recognise the first hand with his back to the camera, he used to let me fettle for him as ’acting-temporary-fifth hand’! We were kept us busy around tapping time (taking a sample) and the sample lad ( a Theaker from Boosbeck, I think) used to curse if the sample was over-quenched and wouldn’t drill! Sid was always impatient – he would wait in the balance room/bait room pacing up an down while Stan (or Derek, the 2nd Chemist) did the analysis – as a lowly 3rd Chemist I was only allowed to do slags and iron samples!”.
Thanks to Eric Johnson and Rodney Begg for the updates.
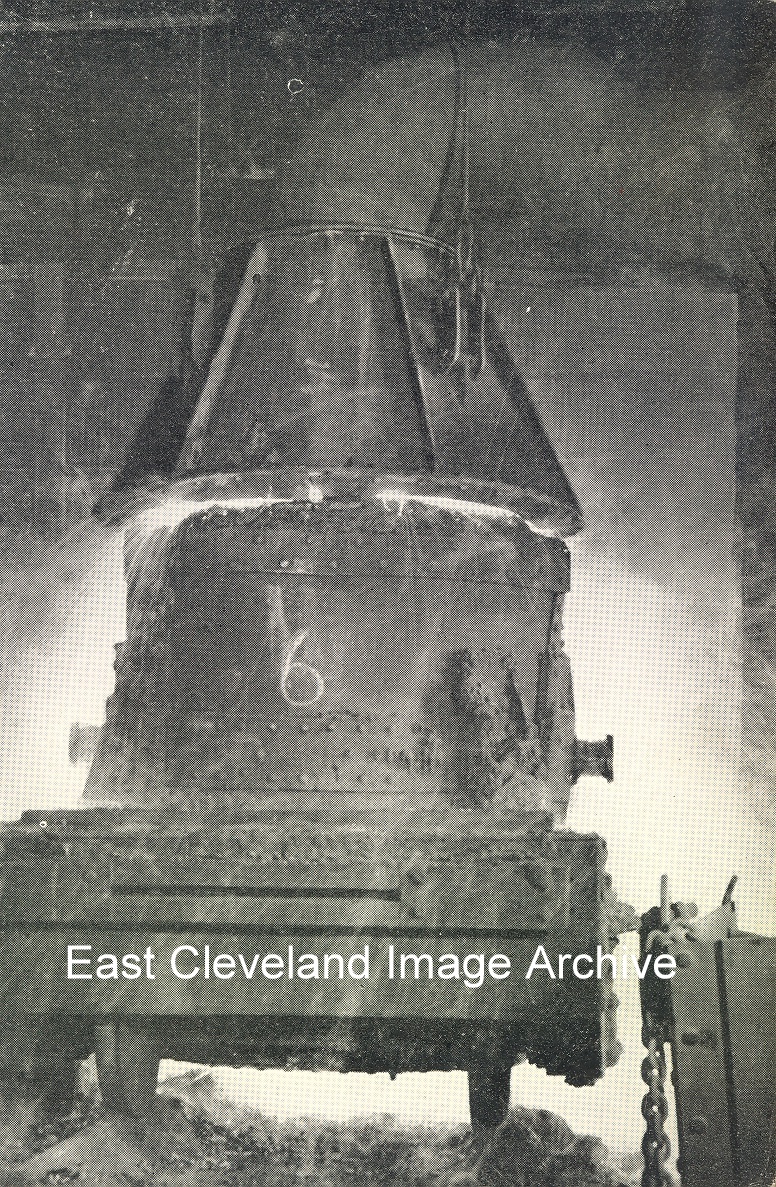
Rodney Begg tells us of de-siliconizing: “When I was at Skinningrove this had fallen out of favour and the equipment lay at the end of the Talbot’s, next to ’D’ furnace. Sound in principle and obviously successful in other areas (this is the basis for Basic Oxygen Steelmaking), it never seemed to catch on at Skinningrove!”.
Thanks to Rodney Begg for this observation.
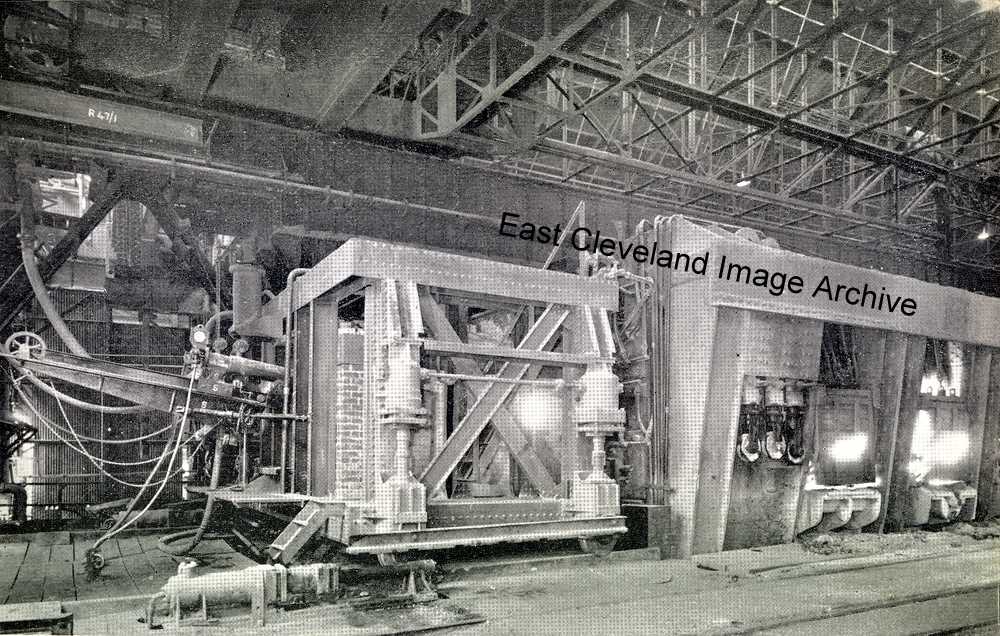
Of the 300 ton steel furnace; Rodney Begg told us: “This is the view I used to get just out of the door of the Shift Laboratory on the Talbot’s; the ’A’ end of a furnace (in this case either ’B’ or ’C’). It is easy to see the difference between this image and the image of the gas-fired one in an earlier post. The burner end is mobile for maintenance and carries much more complex pipe work”.
Thanks to Rodney Begg for the update.
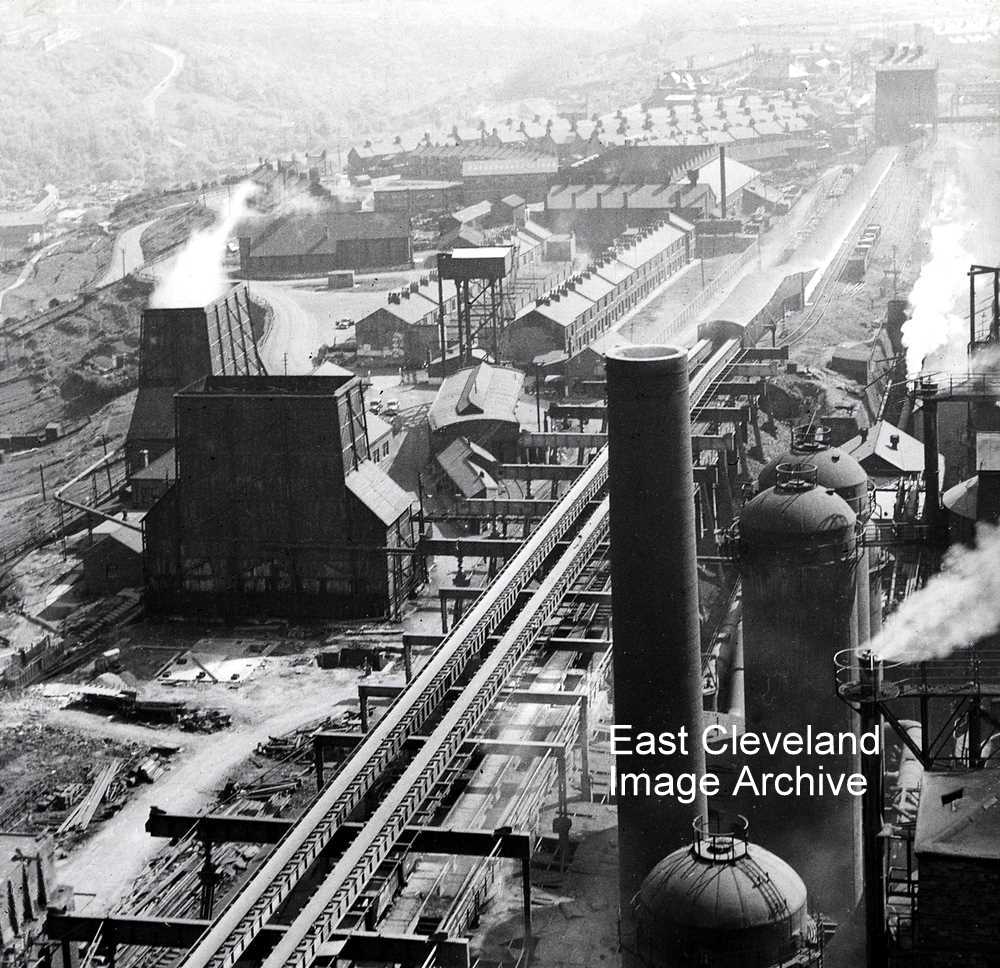
Taken from the top of No. 5 perhaps (maybe during its construction in the 1950’s?). A different view of the iron and steel works, looking inland, and down into the valley; the two rows of Furnace Cottages can be seen. Rodney Begg told us: ”I spent the last 12 years or so of my employment here as a metallurgist in the bottom Test House (just to the right of the water tower and partly hidden by the tall chimney, nearly in the centre of the picture)”.
Thanks to Rodney Begg for the update.
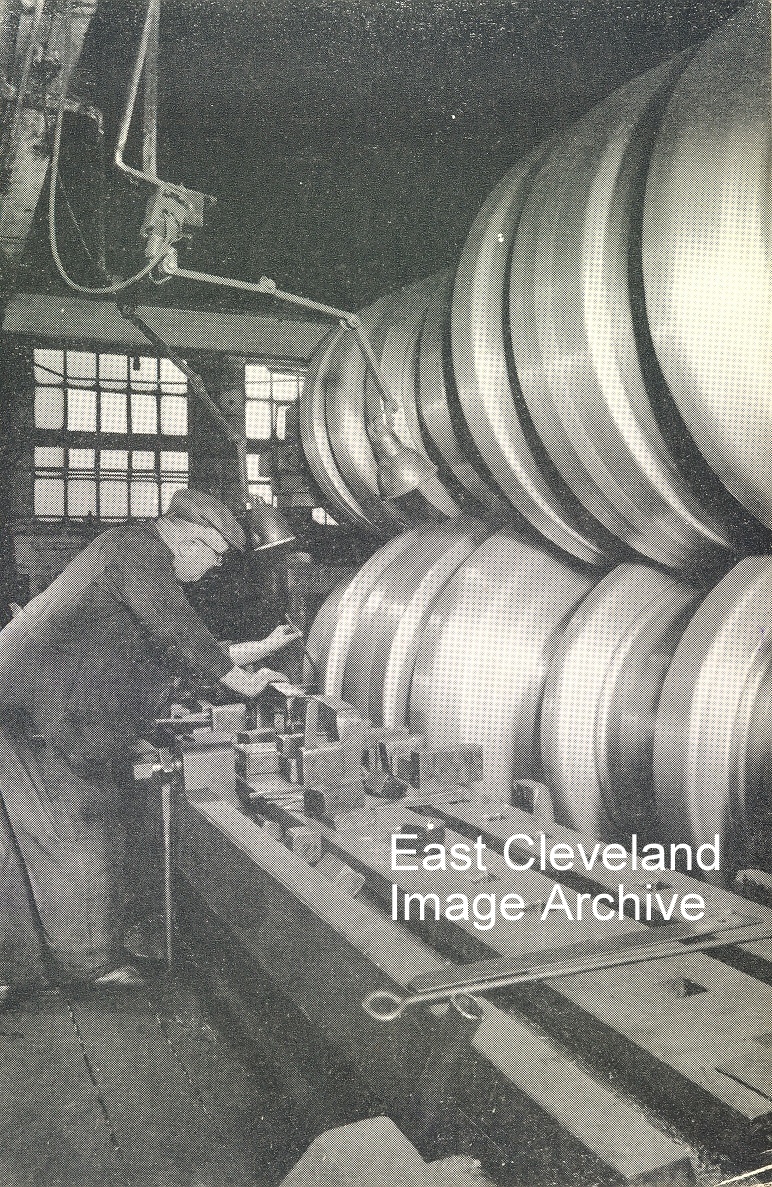
Skinningrove Rolling Mills evolved as completely self-sufficient units, capable of developing the rolls for new sections and manufacturing them from blanks. A number of highly skilled men were involved; from the draughtsmen drawing up the profiles, the pattern makers manufacturing the cut profiles for the roll turners to manufacture. Mike Hore told us: “The roll turner in the photograph is Harry Roberts. I worked with him on the same shift for a number of years before I left the Steel Industry. In addition the photograph was taken in the old roll shop which was situated under the mill arch and under the mill gantry crane. The picture was probably taken in the late 1960’s since the present roll shop came into operation in roughly 1971/72”. Ken Johnson also told us: “I trained as a teacher with Mike Hore. Mike was able to write “Skinningrove” in mirror writing as quickly and efficiently as writing in normal writing.. I wonder if Mike could still do that?”.
Thanks to Mike Hore and Ken Johnson for the updates.
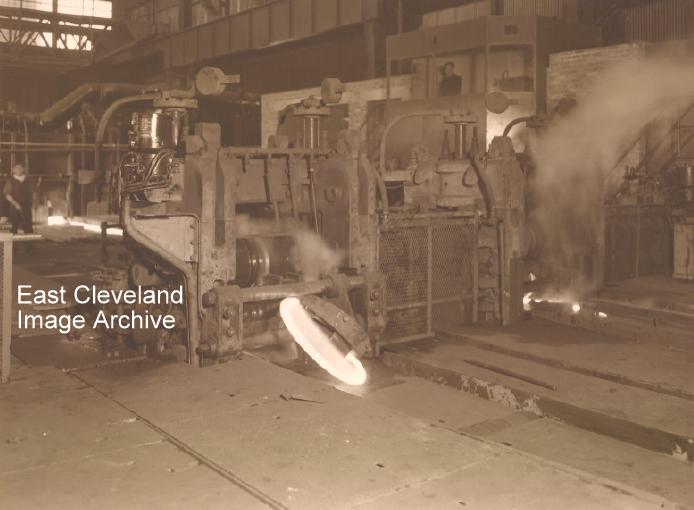
The Archive was not sure which stand this was in the 18” Mill and wondered if someone could enlighten us? Raymond Stonehouse assisted with: “I believe this view is of the Intermediate and Finishing Stands, looking at them from the Saw side (North Sea)”.
Thanks to Raymond Stonehouse for that update.
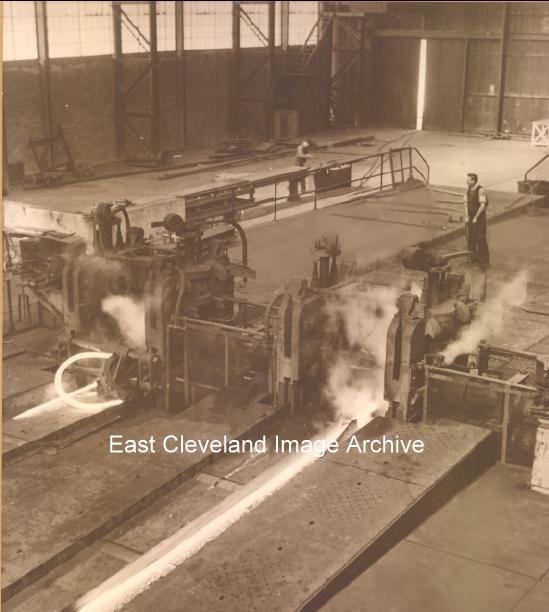
The same applies here, it was almost a taboo place for the uninitiated, the steel used to hurtle around on the mill floor – very scary!
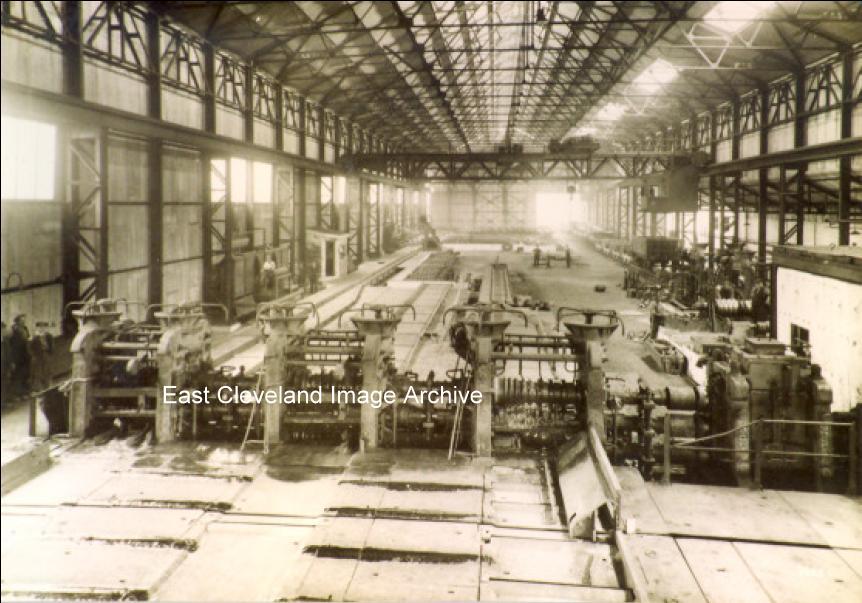
A view down the shop of the 18 inch mill before re-modelling in 1956.
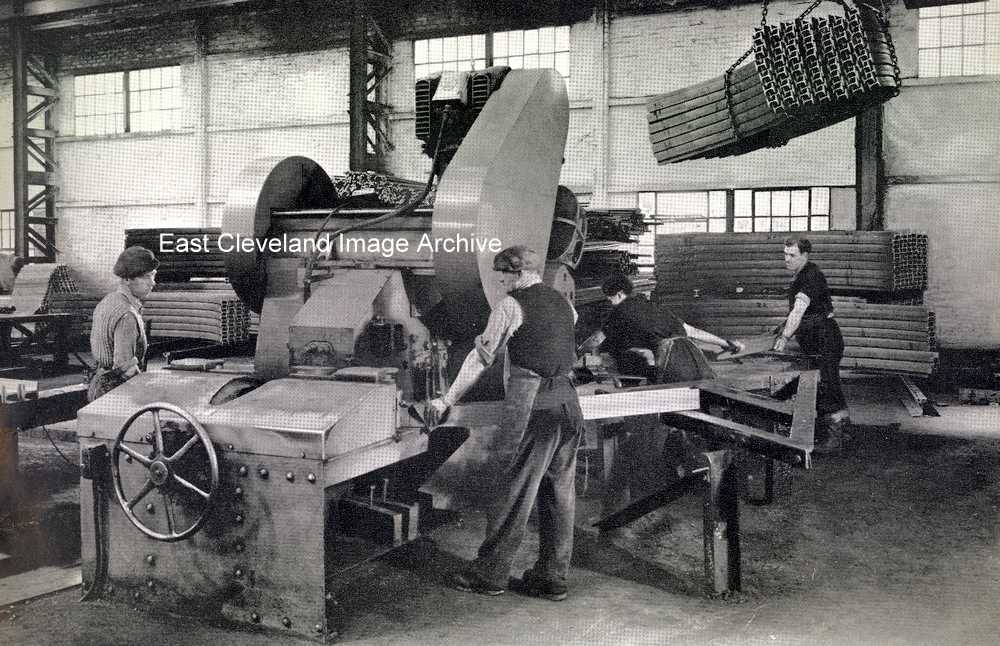
As the mining industry modernised the coal mine in particular moved across to steel for its roof supports and Skinningrove was quick to capitalise on this; the 18” (or Little) Mill being ideally suited to producing small ’H’ beams (or ’I’ beams, if you prefer) and as the order book grew so did the Colliery Arch Department. They were all cold-formed on these rotary bending machines. Frank Bridge advises:”I worked on this very machine back in 1973-1974, a memory worth holding on to. The men I worked with were the hardest grafting and drinking crew you could wish to meet; a truly great bunch of lads”. Eddie Watson adds: “I worked in colliery arch plant B.S.C. Cleveland.from 1975-1986. I worked my way up from stick lad on cropping machine to cambering machine puncher. Very hard work but best times of my life”.
Thanks to Frank Bridge and Eddie Watson for the updates and memories.
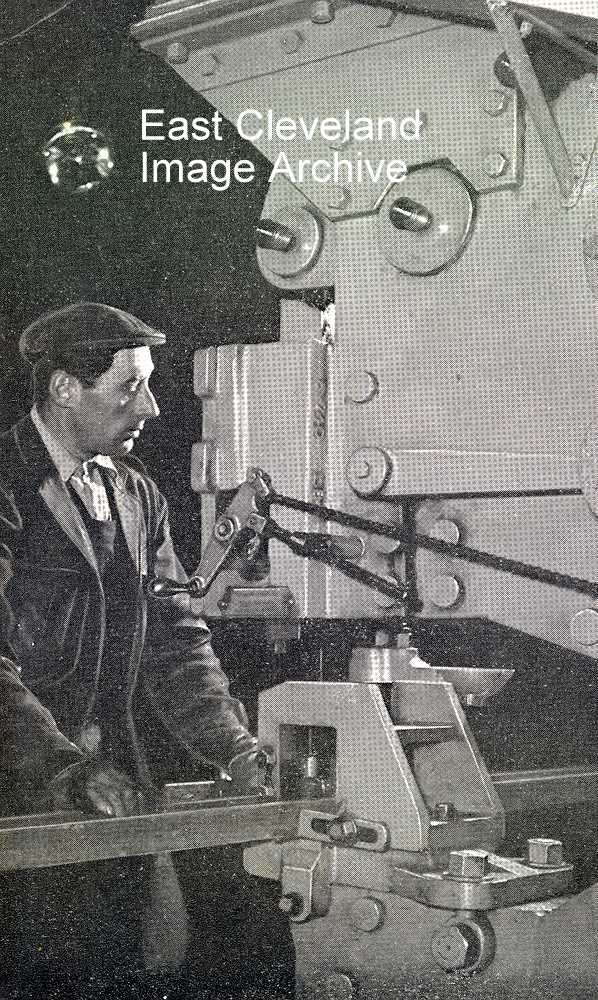
How do you make perfectly finished squared ends to your steel products – with a cropping machine like this.
Image courtesy of the Pem Holliday Collection.
Page 15 of 20« First«...10...1314151617...20...»Last »
|
|
Recent Comments