|
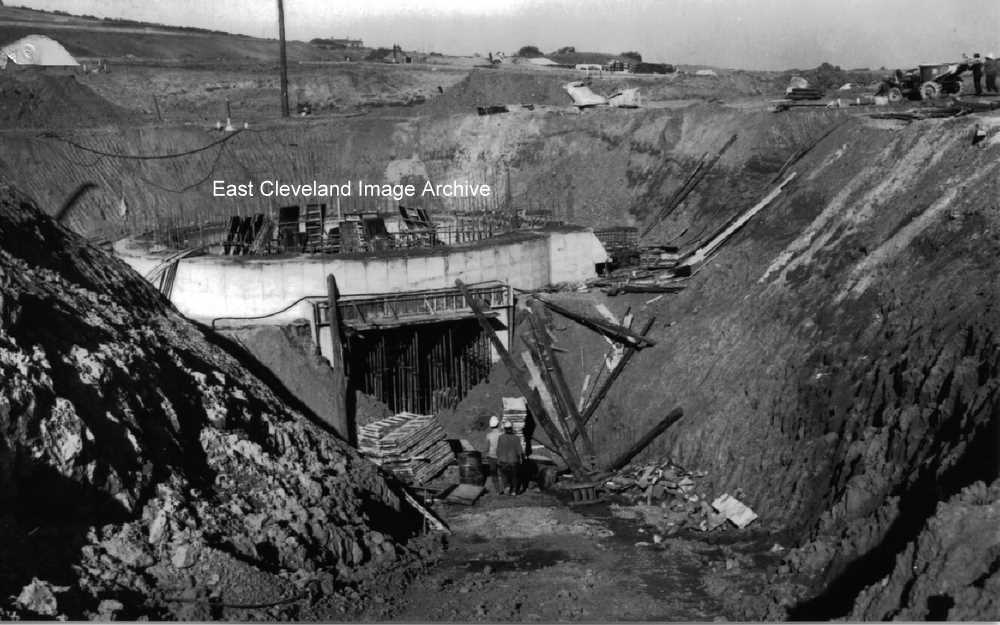
Then we make the top of the shaft nice and pretty ready to build the tower on! Alan Franks has told us: “This is excavating for shuttering to be installed for the Fan drift. ( Fans were sited at the top of this). Myself and two other men spent a week trying to retrieve the shuttering after concrete had been poured and set, with it being in like a valley as you can see, the mud kept sliding down as quick as we could dig out. We saved a few shutter panels but after the week we were told to leave the rest and they were just backfilled and buried.This would be around Christmas time 1969.”
Image and update information courtesy of Alan Franks.
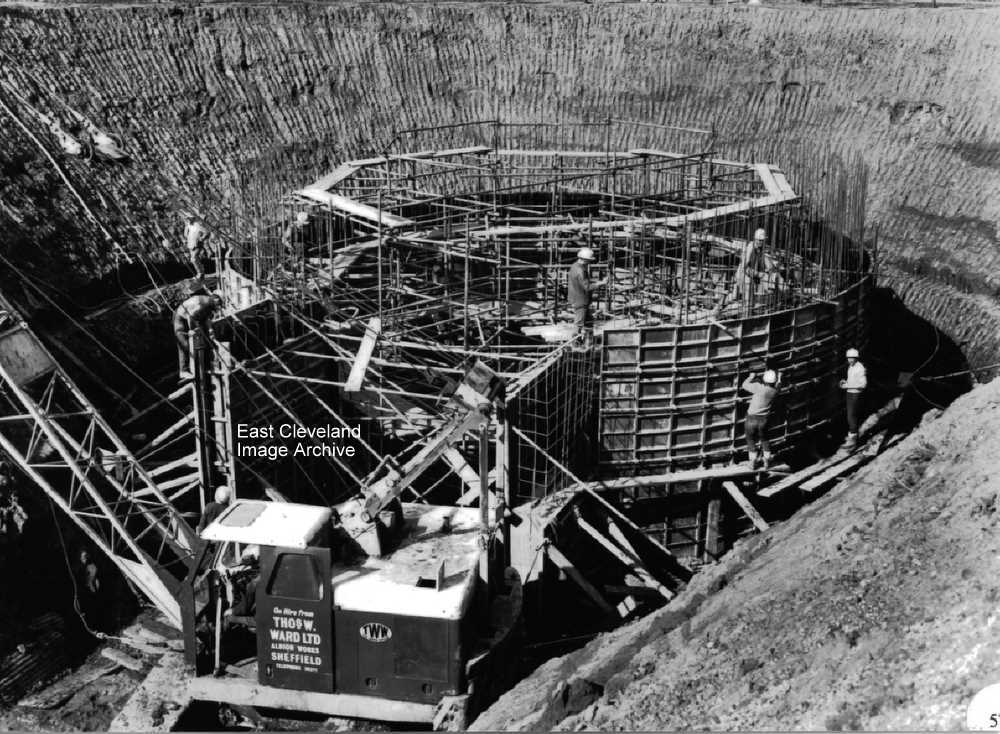
Soon have this finished now; the top of the shaft nearing completion.
Image courtesy of Alan Franks.
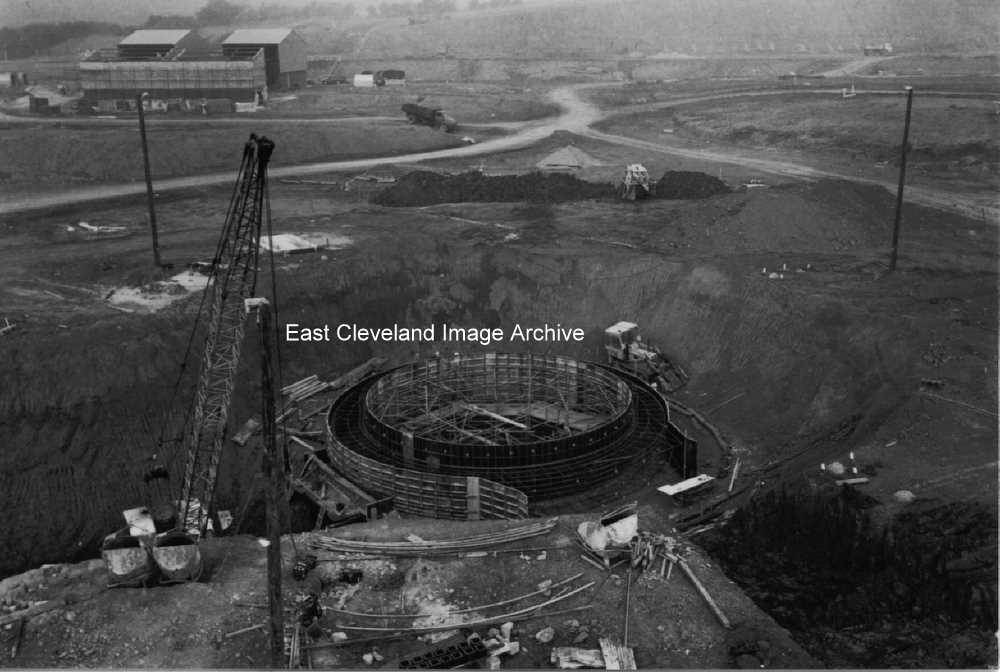
Constructing the top of the shaft, which will be the base of the tower.
Image courtesy of Alan Franks.
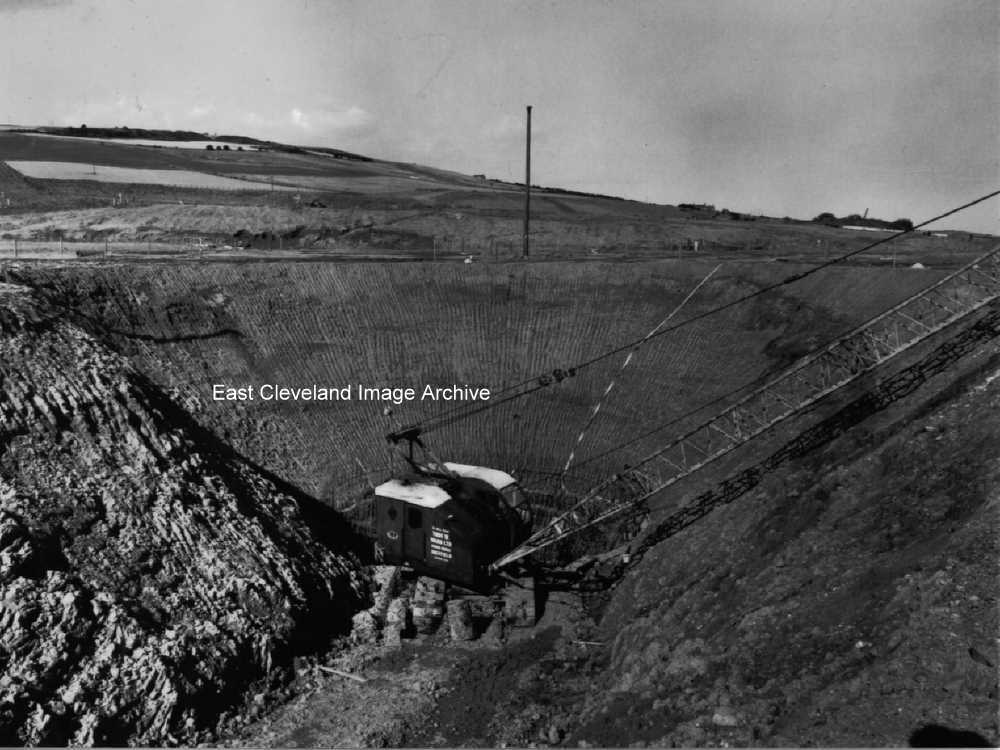
Using a dragline bucket to sculpt the top of the shaft opening.
Image courtesy of Alan Franks.
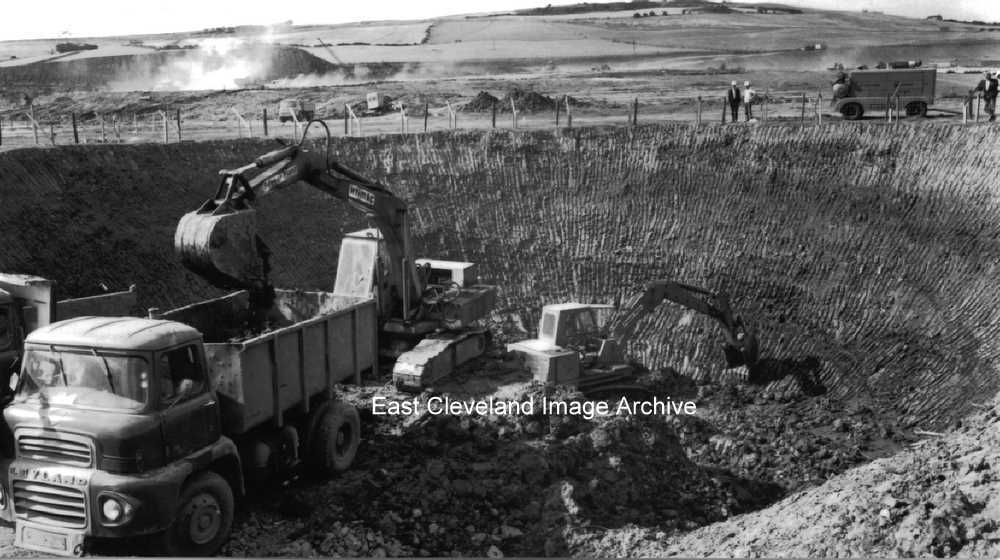
The second bucket fills the lorry.
Image courtesy of Alan Franks.
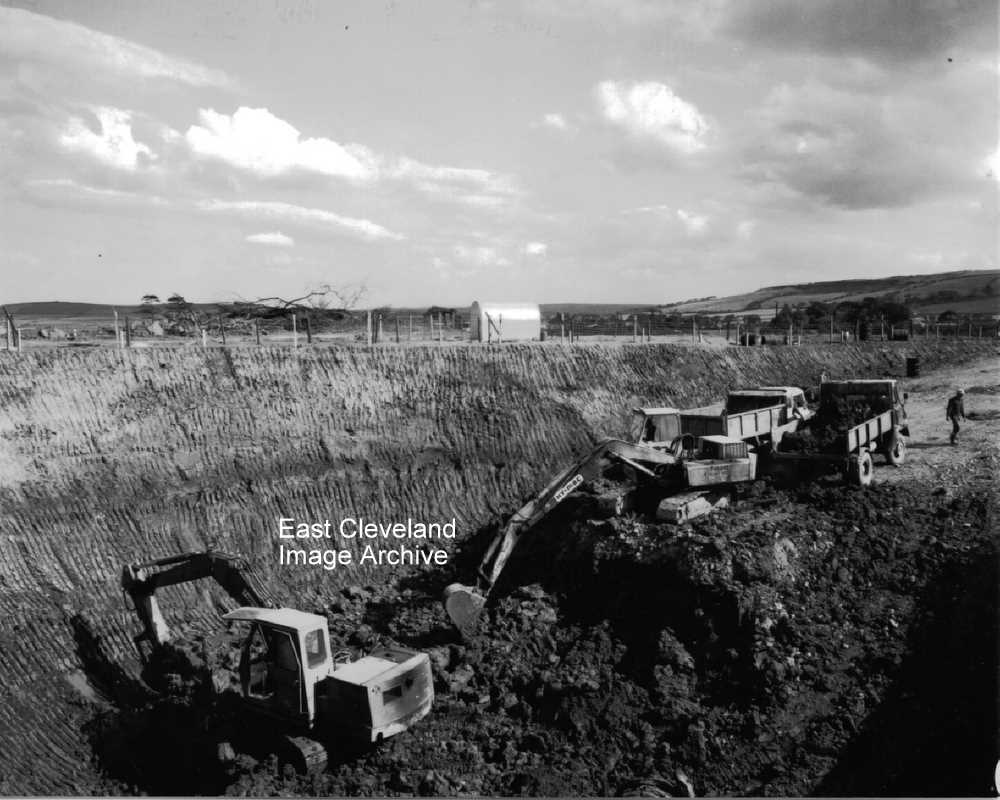
The first bucket digs the hole and puts its load where the second bucket can get it.
Image courtesy of Alan Franks.
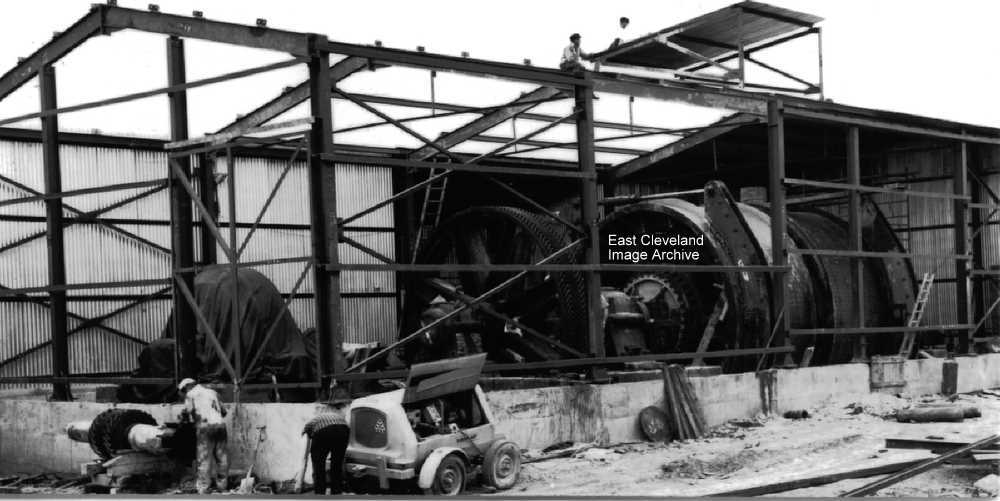
A deep shaft demands powerful haulage gear – and powerful haulage gear demands powerful brakes! – this is one of the winders used for sinking the shafts. These were later dismantled after sinking was complete.
Image and description courtesy of Alan Franks.
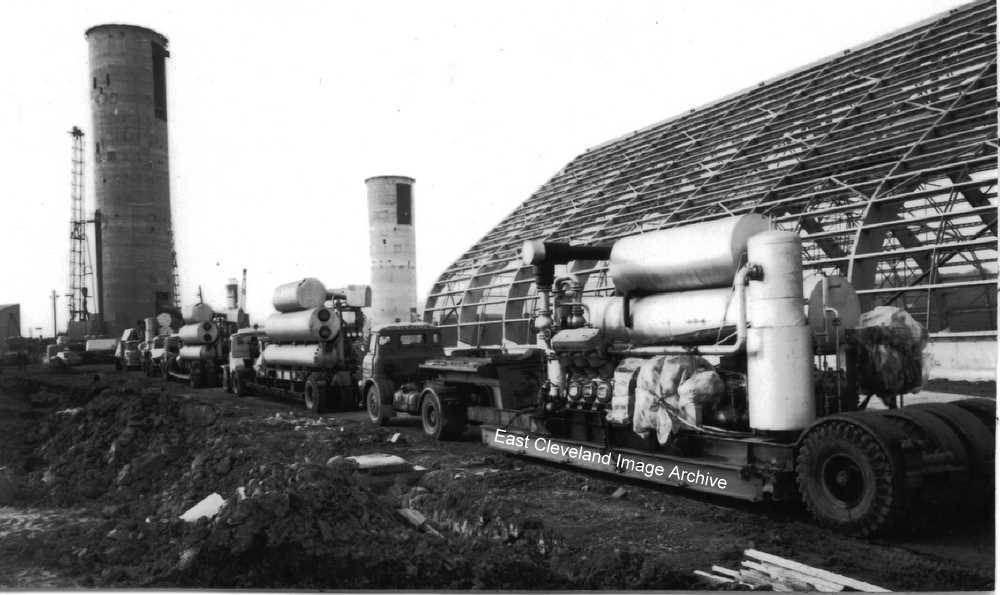
We asked of this image: “Looks like a convoy of big engines – air pumps perhaps?” Aaron Clarke tells us: ”This looks like the freezing equipment which was used in one of the shafts when the ground they were digging down through was too soft to dig through and had to be frozen.” Alan Franks tells us: ”The reason for freezing the ground was because of the amount of water in the Bunter Sandstone at approx 2000 down to 3000 feet down. This was commonly called the ice wall. This was breached while sinking through it, with loads of warm water coming into the shaft. Continuous pumping was done with Pluger pumps enclosed in metal pipes and then 30 feet of gravel and 30 feet of concrete on top. The concrete was later removed by rock breakers ( jiggers ) and hand filled into a cut down Kibble ( big bucket) .While the ice wall was refreezing during this operation the steel lining was installed by a German firm of welders, assisted by us Sinkers. The normal sinking operations recommenced after these operations. This was the Number 1 shaft ( Rock Shaft ), the other shaft Number 2 ( Man Shaft ) was long hole drilled down in stages of about 70 to 80 feet I think there were 32 holes round the shaft floor, then cement and water mix (Grout) was pumped into these holes to seal all cracks in the rock strata to contain the water as in the other shaft. The freezing did the better job of containing the water,also a different steel lining was used ( Tubbings ) these were bolted together and caulked with lead.”
Eric Lindsay tells advises: “Indeed the freeze compressors that ran 24/7 with exemption from the 3 day week electricity cuts. The freeze pipes were spiral drilled through the Bunter Sandstone from a chamber formed in the main shaft just above the sandstone. This sandstone was very permeable horizontally but the opposite vertically. The refrigerated brine was pumped down concentric pipes to provide flow and return from the manifolds in the freeze chamber. After the breach in the ice wall was found when they excavated level with it the shaft was plugged as described and the water pumped through valves. The valves were slowly turned off until all shut and the pressure built up below the plug. If I recall correctly the plug moved up that shaft a short distance. Freezing continued until ice wall hole froze over and until the full depth of shaft had been sunk and lined through the sandstone. The steel tubings came from Head Wrightson I think, in matched rings and were shot blasted on site. The segments were bolted together with lead gaskets. One ring was never paid for as they couldn’t supply me with delivery and weighbridge paper work.
On another subject, the excavated rock hauled out by Noel Carey’s trucks was very saline and the mud on the road was causing cars etc to have rust holes within a year or so. I organised undercoating on site for quite a few guys. ( probably held their cars together for a bit longer !!!
Image courtesy of Alan Franks, thanks to Aaron Clarke, Alan Franks and Eric Lindsay for the updates.
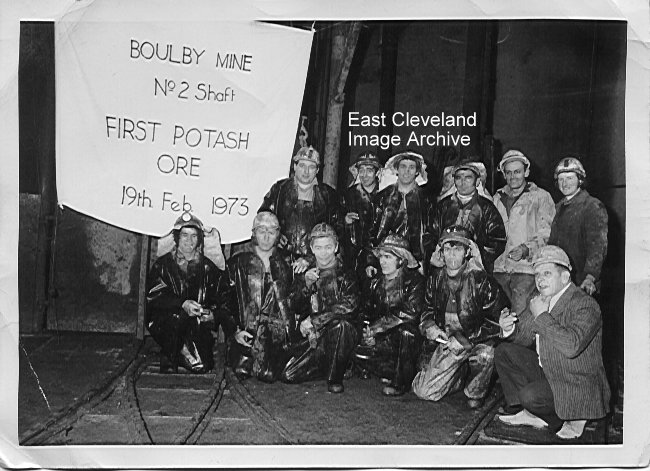
A celebratory group at the bottom of No. 2 Shaft announce the winning of the first potash from the mine on the 19th February 1973.
Back row: ??, ??, Bill Casson, Mick Urban, Alan Scott, Willy Brown.
Front row: Alan Hall, ??, Tommy Wood, ??, ??, Tommy Hornsby.
Could we have assistance with the remaining names?
Image and names to date courtesy of Alan Franks.
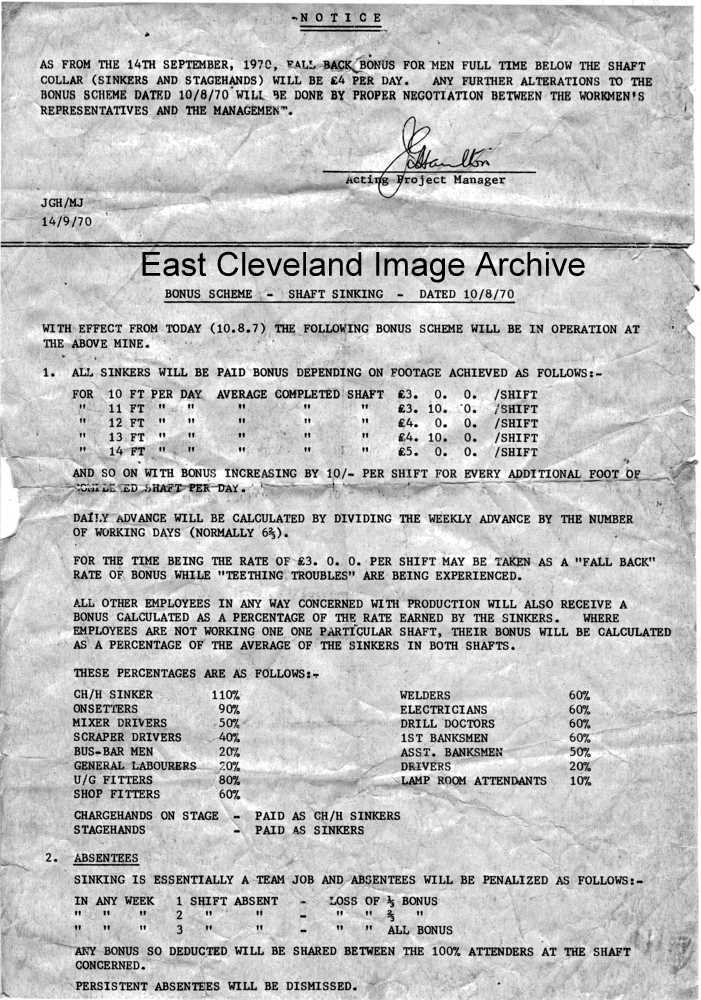
A unique piece of the history of Boulby Potash – the day-to-day dross seldom gets preserved – dating from 1970.
Image courtesy of Alan Franks.
Page 4 of 6« First«...23456»
|
|
Recent Comments